L’anodisation de l’aluminium : un procédé essentiel à comprendre
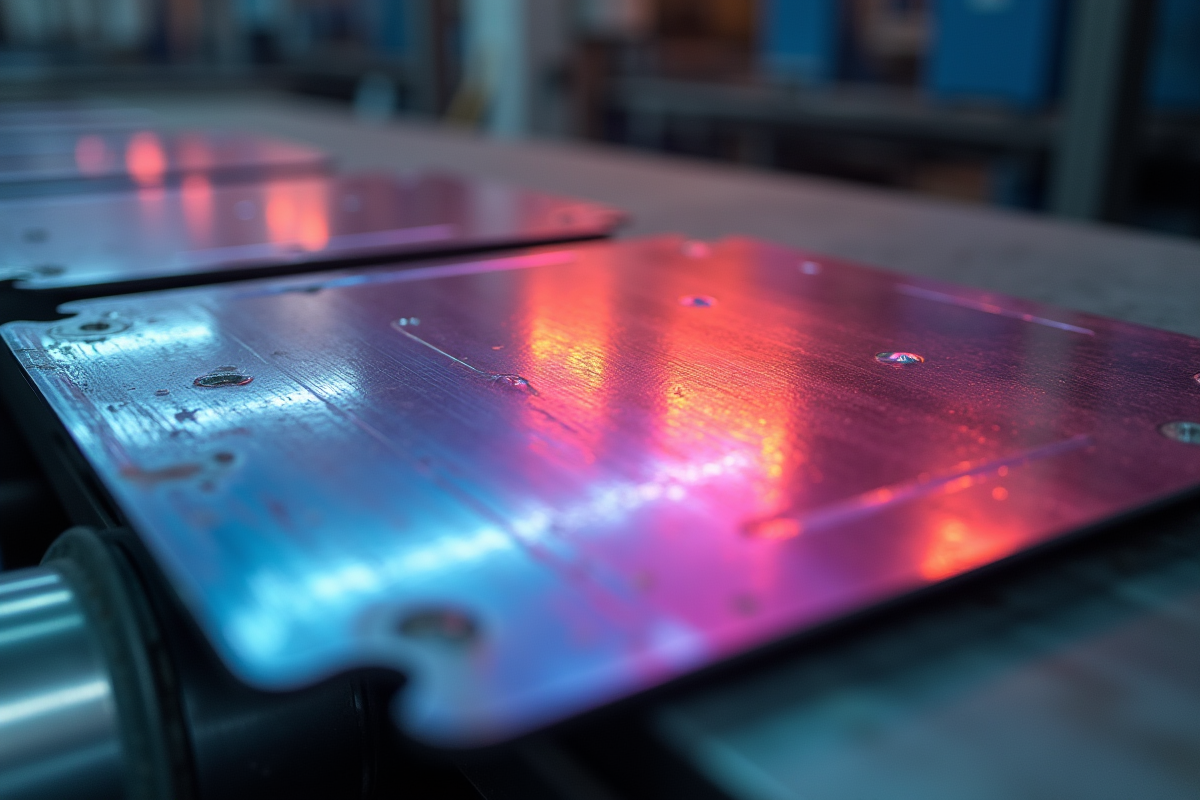
L’aluminium, matériau largement utilisé dans divers secteurs industriels, bénéficie d’une technique spécifique pour améliorer ses propriétés et sa durabilité : l’anodisation. Ce procédé électrochimique permet de créer une couche protectrice d’oxyde sur la surface de l’aluminium, augmentant ainsi sa résistance à la corrosion et à l’usure.
L’anodisation offre aussi des possibilités esthétiques en permettant la coloration de l’aluminium, ce qui le rend encore plus attractif pour des applications dans la construction, l’automobile et l’électronique. Comprendre ce processus est fondamental pour maximiser les performances et la longévité des produits en aluminium.
A voir aussi : C’est quoi Adobe Flash Player ActiveX ?
Plan de l'article
Qu’est-ce que l’anodisation de l’aluminium ?
L’aluminium, matériau incontournable dans de nombreuses industries, bénéficie de propriétés mécaniques exceptionnelles, d’une grande variété d’alliages, d’un faible coût et d’une large disponibilité. Ces caractéristiques en font un choix privilégié pour la fabrication de pièces dans divers secteurs.
L’anodisation est un procédé de traitement de surface industriel qui améliore la durabilité et l’esthétique de l’aluminium. Ce processus électrochimique consiste à immerger la pièce en aluminium dans une solution électrolytique et à appliquer un courant électrique. Cela provoque la formation d’une couche d’oxyde d’aluminium à la surface de la pièce, augmentant ainsi sa résistance à la corrosion et à l’usure.
A lire aussi : Comment contacter le service client d'une entreprise d'informatique ?
Les étapes du processus d’anodisation
- Préparation de la surface : La pièce en aluminium est nettoyée pour éliminer toute impureté.
- Immersion dans la solution électrolytique : L’aluminium est plongé dans une solution d’acide sulfurique ou chromique.
- Application du courant électrique : Un courant électrique est appliqué pour provoquer la formation de la couche d’oxyde.
- Coloration et scellement : Si nécessaire, la pièce peut être colorée avant de sceller la couche d’oxyde pour renforcer sa protection.
Ce procédé permet d’obtenir un produit durable et esthétiquement plaisant, répondant aux exigences des industries les plus rigoureuses. La maîtrise de l’anodisation est essentielle pour maximiser les performances et la longévité des pièces en aluminium.
Pourquoi l’anodisation de l’aluminium est-elle essentielle ?
L’anodisation de l’aluminium joue un rôle clé dans plusieurs secteurs industriels. Industrie aérospatiale, industrie automobile, architecture, biens de consommation et articles ménagers : tous bénéficient des avantages de ce procédé.
- Industrie aérospatiale : L’anodisation est utilisée pour améliorer la résistance à la corrosion des composants aéronautiques. Les pièces anodisées sont plus durables, ce qui est fondamental pour les appareils volant à haute altitude et soumis à des conditions extrêmes.
- Industrie automobile : Les pièces de carrosserie et les éléments structurels anodisés présentent une meilleure résistance à l’usure et à la corrosion, prolongeant ainsi la durée de vie des véhicules.
- Architecture : Les structures en aluminium anodisé, telles que les façades et les fenêtres, offrent une esthétique supérieure tout en résistant aux intempéries et à la pollution.
- Biens de consommation : Les appareils électroménagers et les gadgets anodisés sont non seulement plus attrayants, mais aussi plus robustes et résistants aux rayures.
- Articles ménagers : Les ustensiles de cuisine en aluminium anodisé, comme les casseroles et poêles, offrent une meilleure conductivité thermique et une résistance accrue aux taches.
En améliorant la résistance à la corrosion et en offrant une protection esthétique, l’anodisation prolonge la durée de vie des produits et réduit les coûts de maintenance. Dans un monde où la durabilité et l’efficacité sont primordiales, comprendre et maîtriser ce procédé est indispensable pour rester compétitif. Les industries doivent ainsi intégrer l’anodisation dans leurs processus de fabrication pour améliorer la qualité et la performance de leurs produits.
Comment fonctionne le processus d’anodisation de l’aluminium ?
L’anodisation de l’aluminium repose sur un procédé électrochimique qui transforme la surface du métal en une couche d’oxyde protectrice. Ce processus est divisé en plusieurs types, chacun ayant ses spécificités.
Les types d’anodisation
Type I (anodisation à l’acide chromique) : Utilise l’acide chromique comme électrolyte et produit une couche d’oxyde protectrice d’environ 0,08 à 0,25 microns. Ce type est particulièrement utilisé pour des applications nécessitant une couche mince mais efficace.
Type II (anodisation à l’acide sulfurique) : Utilise l’acide sulfurique comme électrolyte et produit une couche d’oxyde plus épaisse (2,54 à 25 microns) que le type I. Ce type est fréquemment employé pour des pièces nécessitant une protection accrue contre la corrosion.
Type III (anodisation à couche dure) : Utilise une tension plus élevée et de l’acide sulfurique pour produire une couche d’oxyde de 25 à 150 microns. Ce type est destiné aux applications où une résistance extrême à l’usure et à la corrosion est nécessaire.
Le processus en détail
Le processus d’anodisation commence par une préparation de la surface, où la pièce en aluminium est nettoyée pour éliminer les impuretés. La pièce est immergée dans un électrolyte approprié (acide chromique ou sulfurique) et un courant électrique est appliqué, transformant la surface en une couche d’oxyde d’aluminium.
- Préparation : Nettoyage et dégraissage de la pièce.
- Électrolyse : Immersion dans une solution d’acide et application d’un courant électrique.
- Rinçage et coloration : Rinçage à l’eau et, si nécessaire, coloration pour des fins esthétiques.
- Scellement : Scellement de la couche d’oxyde pour améliorer la résistance à la corrosion.
Ce processus améliore significativement les propriétés de l’aluminium, en augmentant sa résistance à la corrosion et en permettant diverses finitions esthétiques selon les besoins industriels.
Les avantages et inconvénients de l’aluminium anodisé
Avantages
- Résistance à la corrosion : L’anodisation augmente considérablement la résistance de l’aluminium à la corrosion en formant une couche protectrice d’oxyde.
- Durabilité : Ce traitement de surface confère une grande durabilité au matériau, le rendant idéal pour des applications extérieures.
- Esthétique : La possibilité de coloration offre une large gamme de finitions esthétiques, répondant aux besoins variés des industries de la mode et de la décoration.
- Respect de l’environnement : Le procédé d’anodisation, lorsqu’il est bien contrôlé, génère moins de déchets toxiques comparé à d’autres traitements de surface.
Inconvénients
- Coût initial : Les installations nécessaires pour le processus d’anodisation peuvent représenter un investissement conséquent.
- Fragilité de la couche anodisée : Bien que résistante à la corrosion, cette couche peut être sujette à des fissures ou des écaillures si elle est soumise à des chocs mécaniques importants.
- Limitation sur certains alliages : L’anodisation n’est pas aussi efficace sur tous les alliages d’aluminium, notamment les séries 2000 et 7000, qui peuvent présenter des problèmes de coloration ou de qualité de la couche anodisée.
Alliage | Caractéristiques |
---|---|
Série 1000 (aluminium pur) | Conductivité électrique élevée, excellente résistance à la corrosion |
Série 3000 (alliages aluminium-manganèse) | Bonne formabilité, excellente résistance à la corrosion |
Série 5000 (alliages aluminium-magnésium) | Rapport résistance/poids élevé, excellente résistance à la corrosion |
L’anodisation de l’aluminium reste une technique de choix pour de nombreuses industries, allant de l’aérospatiale à l’architecture, en passant par les biens de consommation. Considérez les spécificités des alliages pour optimiser les résultats.